Podiatrists work daily to improve their patients’ posture and mobility. Insoles play an important role in this effort, but making and ordering them is time-consuming. Methods, such as manual adjustments or CNC milling, involve dust, noise and waste. Fortunately, there is an innovative solution: 3D printed soles. This will save you time, improve efficiency and keep more control over your production process.
The problem: time-consuming production and dependency
Many podiatrists run into the same problems when producing or sourcing insoles:
- Time-intensive manual labor
Sanding, gluing and finishing soles is time-consuming and requires precision. This comes at the expense of time that can be spent on patient care. - Dependence on external suppliers
When soles are outsourced to an outside partner, it means waiting time. Delivery can take days, and if there is an error in sizing or finishing, the entire order must be redone. - Lots of waste and unhealthy working conditions
CNC milling works with large blocks of material of which up to 95 percent becomes waste. In addition, the process creates a lot of dust and chemical fumes from adhesives and coatings. This is not only bad for the environment, but also for the health of the handler.
How 3D printed insoles save time
With a 3D printer for soles, such as the MODULA from PodoPrinter , you bring all production in-house. This provides significant benefits:
- Automation of the production process
The 3D printer makes soles without manual sanding or gluing. This saves time and reduces physical strain. - Faster delivery time and less dependency
Because you control production yourself, you no longer have to wait for outside suppliers. This means that soles are ready for use immediately, without additional transportation costs or long delivery times. - Consistent quality without manual errors
Manual adjustments lead to slight variations in the finish of soles. With a 3D printer, each pair is printed identically and exactly to specification, improving quality and fit. - Cleaner and healthier work environment
A 3D printer operates without milling dust and harmful glue fumes. This makes for a safer workplace and less need for expensive exhaust systems. - Less waste and lower costs
Instead of milling out a large block of material, the printer uses exactly the amount of raw material needed. This not only saves costs, but is also more sustainable.
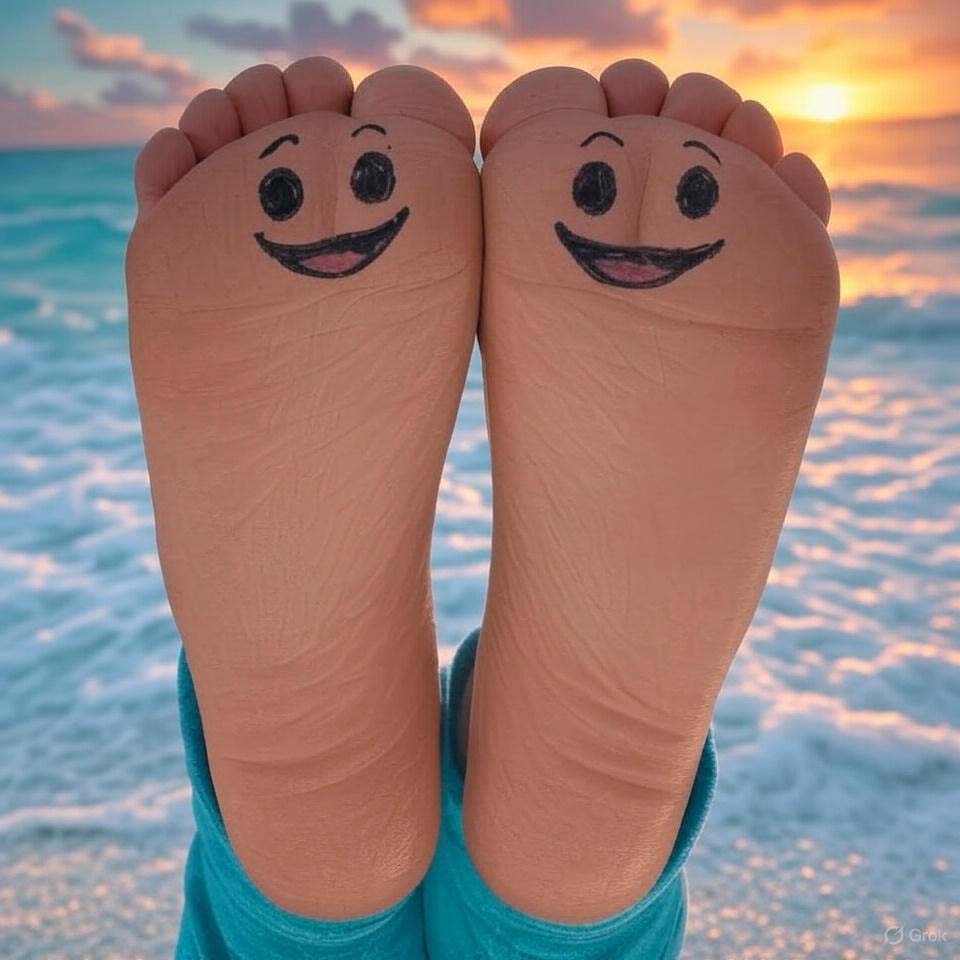
What does this mean for daily practice?
By switching to 3D printed soles, podiatrists can work more efficiently and help more patients without employing additional staff. The time savings add up to 20 percent, which amounts to a full working day per week. This gives room to schedule more consultations or just reduce the workload.
In addition, 3D printing offers new possibilities. For example, it is possible to integrate different hardnesses within one sole, allowing for even better support. Patient data can also be printed directly into the sole, so there is never any confusion about which soles belong to which patient.
More control and less loss of time
Innovations in healthcare increasingly revolve around efficiency and customization. 3D printed soles fit perfectly within this trend. They make production faster, cleaner and less dependent on external parties.
For podiatrists looking to optimize their workflow, reduce costs and create a healthier work environment, 3D printing is a logical next step. The move means not only more efficient practice operations, but also an improved patient experience.
Want more control over your production and less time wasted on manual adjustments? Then 3D printing is the future for your practice.
Wondering what PodoPrinter can do for your practice?
Would you also like to benefit from the advantages of 3D printed soles? Then contact us for a no-obligation demonstration of our Modula.